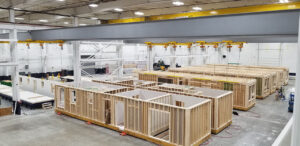
Prefabrication is changing the current paradigm in the construction and building industry. Modular, factory-constructed built environments can be produced significantly faster, more economically and often safer than traditional field construction. Indeed, a report from industry advisory group McKinsey & Co. found that “modular construction can cut schedule by 20–50 percent and costs by 20 percent,” positioning it to significantly disrupt traditional construction and real-estate sectors.
So it’s no wonder that, with a Compound Annual Growth Rate (CAGR) of over 8% expected through 2025, the construction industry is increasingly turning to or considering the modular construction.
One particular example comes from the education sector where the demand for classrooms and training facilities has been skyrocketing. The COVID-19 pandemic has created a critical need to quickly establish healthy and safe learning spaces. For example, social distancing —a necessity during the pandemic—requires significantly more square footage to accommodate the same number of staff and students or trainees.
Modular educational environments can be built and deployed rapidly to extend available space while incorporating health and safety features like enhanced air flow and ventilation. Construction of modular educational units, however, can be more complex than residential or other spaces, requiring considerably more electrical work such as dedicated circuitry and IT components. Further, security concerns are more intense and heavily regulated.
Another complication: modular manufacturers are not always optimized for producing these factory-built environments. Traditional material handling systems that move massive assemblies through the facility can create as many problems as they solve. To get the most out of prefabrication, these manufacturing facilities need to ensure that every modular construction tool successfully capitalizes on the strengths of the prefab process. The solution is a material handling system that has been proven to support modular methodologies: air casters.
Air casters rise above other material handling systems
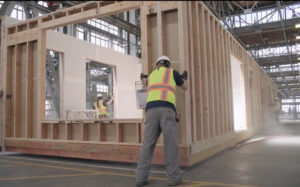
Air caster systems use standard compressed air to inflate bags beneath the structure or assembly to be moved. Once the bag reaches capacity, air evenly leaks between the bag and the floor until it forms an ultrathin film of air the thickness of a business card (0.003” to 0.005”). Air casters also fit within the footprint of the load, can move in any direction, and can rotate in place.
Functionally, air casters work just like hovercraft or the puck on an air hockey table. With a friction coefficient of less than one percent, even a single operator exerting no more than 5 to 25 pounds of force can easily move and precisely position a load weighing as much as 5,000 pounds. Moving heavier loads requires only a modest number of additional air caster modules and operators. Jason Carter, president of advisory firm The Mod Coach, which works with manufacturers to implement and optimize modular factory design, advises clients to assemble a small team of operators and spotters dedicated to moving oversize modular educational assemblies. Since the move takes minimal time, the team can return to its workstations quickly.
Air casters are extremely efficient at distributing the weight of the load evenly over the floor surface resulting in an extraordinarily low floor loading of around 25 psi. Contrast that figure with the floor loading equivalent to thousands of psi associated with wheeled vehicles. The latter can and will damage floors while air casters do not, even when moving massive boxes.
Benefits of air casters for facility engineers

Air casters power a degree of plant design flexibility and adaptability that isn’t possible with other material handling systems. “Perhaps the fundamental benefit of air casters is the ability to design creative plants,” Carter says. Air casters benefit production processes in five key areas:
1. Air casters make it easier to move large assemblies compared to other systems.
“One of the most difficult and costly challenges in prefab is moving large volumetric pieces,” says John McElroy, process engineering manager at Plant Prefab, which designs and builds custom, high-quality modular buildings. McElroy explains that modular assemblies are cumbersome to move and require larger and more expensive material handling equipment like cranes, forklifts, or chain systems. Worse, the cost of the material handling system increases at a disproportionate rate as the size and weight of the assembly grows. “As a crane needs to become bigger to pick up heavier boxes, the cost increase for the crane to handle more weight is not a linear scale relative to the weight,” McElroy explains. “The cost increases almost on an exponential scale.”
Even the drag chain systems embedded at many older modular construction facilities impose significant costs. They must be massive to move large, prefabricated structures, which adds expense, slows the process, and erodes productivity.An air caster system, by contrast, is based on a single principle: compressed air motion. Operators can move heavier items, including those weighing tens of tons, just by adding more air caster modules. Here, the cost progression is linear relative to weight increases.The benefits are not just economic. Air casters are small and lightweight, which makes them easier to manage and operate. They require no certified operators and only minimal training for use. “Just grab a few more casters, put some air into them, and boom, move,” says McElroy. “It’s a highly important part of the overall process.”
2. Air casters require less space, so facilities can fit more production into the same area.
Because air casters fit within the footprint of the structure being moved, little-to-no additional space is required for maneuvering through a facility. Alternatives such as forklifts need extensive room to maneuver, twist or turn, so they must be included in planning the floor layout, particularly an educational built environment. Since prefab modules for education and training are especially large, they require unusually large forklifts and significantly more space to maneuver.“Since you lose production space with forklifts,” says McElroy, “your ability to have the same throughput in the same square footage of building is reduced.”
By fitting more equipment into less space, manufacturers can maximize production capacity. They can also eliminate or substantially reduce common form of wastes, like excess travel and motion – a key objective for any manufacturer implementing lean manufacturing methodologies.
3. Air casters enable operators to reconfigure plant layouts easily.
With cranes or chains in particular, manufacturing facilities may be limited to a specific production layout, usually a straight line, for moving assemblies from station to station. With air casters, a facility could easily switch to a U-shaped production line that is speedier and more efficient.“Speed gains from air casters are really helpful,” confirms Carter. Indeed, for modular educational environments, speed and efficiency gains can help offset productivity losses since the production process is often more laborious and involved than simpler construction projects. “We can even move them with people inside them,” Carter says. “You have so much freedom because you’re not connected to anything. If needed, you can put everything in a bay and put it back into the line at any point or time.”
4. Air casters reduce injury risk in the movement of modular educational environments.
Cranes, forklifts, and chains all impose specific safety hazards. Chains in particular present an omnipresent tripping hazard. At a modular construction facility, such a system would require a massive chain going through any number of stations along a length stretching hundreds of feet. “You know it’s there, but there’s no way to go around it,” Carter says.Worse, the U.S. Bureau of Labor Statistics has found that upwards of 35,000 injuries occur every year from workers who become caught in moving machinery. Cranes and forklifts can also be deadly. An average of 41 crane-related fatalities occur annually in the U.S,; forklift accidents in the U.S. average 85 fatalities and nearly 35,000 injuries annually.Thanks to ease of movement, air casters impose less risk of strain-related injuries, and because they raise loads no more than a few inches, the risk of injury due to falling loads is eliminated. A small number of spotters can ensure no equipment or personnel are struck as the load moves from station to station.
5. Air casters strengthen manufacturer resilience against COVID-19 and other unforeseen disruptions.
Efficiency gains can yield secondary benefits. “When you’re down with labor because you’re pulling guys who have tested positive [for COVID-19], we can move these assemblies with a lot less people,” says Carter.Such flexibility can also be helpful in dealing with pandemic-caused supply shortages. A manufacturer who produces boxes with incomplete supply product because of supply chain issues can move the assembly out of the way and eventually back in line without disruption or line stoppage.
Successful construction of educational environments
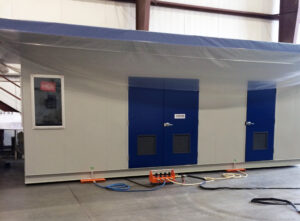
Ultimately, the measure of success for modular built environments is their ability to serve their intended purpose—a reality particularly applicable to educational modular facilities. “Education design is, ultimately, the slave of education outcomes. Set the learning outcomes that students and teachers want to achieve, then work backwards to design a space that delivers those outcomes,” recommends a report from interior design firm Roar that analyzes issues educators will face when they return to in-person instruction after the coronavirus pandemic abates.
That requires a fabrication process that is highly efficient, safe, and reliable. “We want to be like automotive for the construction market,” says Plant Prefab’s McElroy. “In order for us to do that, we need a process that can build these components in a highly efficient manner. Air casters lower the cost and enable us to provide superior products to the masses.”
Carter from Mod Coach agrees: “Combining happy workers with a good system ultimately yields better and stronger products.”
Rising demand for today’s education and training is changing the face of construction by prompting more reliance on prefabrication. To make the most of a modular, pop-up approach to constructing educational built environments, manufacturers must have the right tools to power a good system. Flexibility and on-demand movement provided by air casters can enhance the schedule and cost savings that modular construction is designed to deliver, ultimately producing successful training and education facilities on time and on budget.